Load Cells and Force Sensors
When you’re in the market for load cells (force transducers), custom weighing systems and first-rate load cell repair, Load Cell Central is the name you can rely on.
Load Cell Experts Since 1985
We’ve been earning our reputation as an industry leader since 1985 by putting our customers first. With Load Cell Central, you’ll receive comprehensive service to help you navigate our complete range of load cell solutions.
Load Cell Types
Special Applications
How a Load Cell Works
A load cell is a type of force transducer (force sensor). It converts force exerted on the load cell, such as tension, compression, or pressure, into an electrical signal. The strength of the signal is directly proportional to the force applied.
Strain gauge load cells are the most commonly used type of load cells in industrial applications. The body (or "spring element") of an industrial load cell is composed of a minimally flexible metal on which strain gauges have been secured. When force is applied, the spring element deforms slightly but is elastic enough to return to its original shape.
As the shape of the spring element changes, so does the shape of the strain gauges attached to it, thereby either increasing or decreasing their electrical resistance. When a current is passed through the strain gauges, this resistance variation will be reflected in the measured voltage output. Since this change in output is proportional to the amount of weight applied, the weight of the object can then be determined from the change in voltage.
In order for the spring element to deflect without permanent deformation, the amount of deflection must be minimal. Calculations based on the tiny resistance change of one strain gauge are not highly accurate and can be subject to error. To compensate for this, and allow for a very high degree of accuracy in a load cell, multiple strain gauges are used. Set in a Wheatstone bridge configuration (balanced when no load is applied) the overall change in resistance across all 4 strain gauges can be determined using Ohm's law and the equation below.
VO = | R3 | – | R2 | × VEX | ||
(R3 + R4) | (R1 + R2) |
Choosing a Load Cell by Type
Beam Load Cells
These load cells can be found in vessel/tank weighing and floor scales. There are 3 major types, bending beam, single-ended shear beam, and double-ended shear beam. The single-ended model is mounted on one end and force is applied to the opposite end. The double-ended load cell is mounted on both ends and force is applied to the middle of the load cell. Bending beam load cells are economical and ideally used for lower-capacity applications. Shear beam load cells are best for medium to high capacity weighing double-ended shear beam load cells being intended for higher capacities.
Single Point (binocular)
These single point compression load cells are a lower-capacity load cells. They are perfectly designed for deli scales, bench scales, and checkweighing applications as they are moment compensated load cells. The cell body is modified and the gauges are arranged so that they allow for load placement anywhere on a scale platform and they will return an accurate value.
Pancake (shear web type)
Pancake load cells are often seen in a manufacturing environment, such as car manufacturing. They are used to measure durability and product failure limits in destructive testing. They are also ideal for verifying force measurement in press applications. These cells can be sandwiched between two components for compression or used in tension via threaded holes.
Canister (column)
The canister load cell is the earliest load cell design. This configuration is best suited to higher capacities. They work well in heavy-duty applications such as truck scales and railroad scales. Canister load cells are available in compression-only or tension/compression. As with shear web load cells, some are designed with threads for pulling applications.
S-Type
These S-type load cells are typically found in hanging scales or suspended vessel weighing applications and can be used in both tension and compression applications. They can be suspended from shackles and pulled in tension or mounted between two items via the top and bottom threads and compressed.
Tension Link
These versatile force transducers (load cells) are specialized for measuring in-line tension forces. Tension link load cells are available in a wide range of capacities, tension link load cells are also customizable for extremely heavy applications. These cells are often used for mooring and submersible testing, crane scales, and towing/pull force measurement.
Load Pin
Load pins replace a pin or axle on which force is applied. The design and structure of these cells are highly customizable and can be used at very high capacities.
Thru-Hole Load Cells
These thru-hole load cells are well suited for anchor and fastener testing and boat mooring tests. This extremely versatile load cell is utilized in tension and compression. It can be installed between two parts to measure compression or pulled from opposite directions like the link in a chain to measure tension. They can also be threaded onto a part, such as a bolting mechanism, to measure force.
Select a Load Cell by Capacity
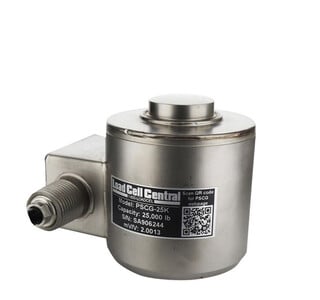
Low Capacity Load Cells
Capacities from 25 grams to 150 Pounds
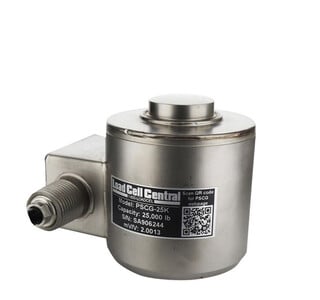
Mid-Range Load Cells
Capacities from 200 to 20,000 Pounds
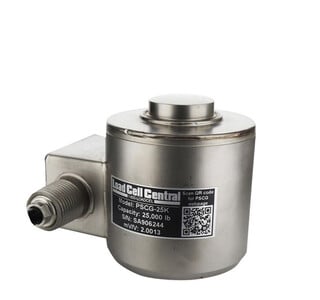
High Capacity Load Cells
Capacities from 25,000 to 1 million Pounds